No process is perfect; there’s always room to improve. Unfortunately, many teams have no way to identify, test, and deploy the changes they make, meaning each tweak is a roll of the dice.
The savings can be massive, but you need a continuous improvement program to make sure that the changes you make won’t make your operations a whole lot harder.
“1 in 10 improvements save money… [each saving, on average,] $31,043 in its first year of implementation.
1 in 4 improvements save time… [each saving, on average,] 270 hours in its first year of implementation.”
– KaiNexus, The ROI of Continuous Improvement
Most successful changes will also make your employees’ jobs easier (and more enjoyable) to perform. You’ll be saving time and money, but you’ll also be getting far better value out of your current efforts and operations.
However, I’m getting ahead of myself. Let’s start from the top.
- What is continuous improvement?
- Incremental vs. breakthrough improvements
- The benefits of continuous improvement
- How to deploy continuous improvement
- Improvement resources to dive deeper
What is continuous improvement?
Ever corrected a spelling mistake in your processes or manuals? How about adding a new step to qualify a task that wasn’t recorded before? What about updating your method to take advantage of better tools or software?
These are a few examples of continuous improvement.
Continuous improvement is a method to make sure that your processes, methods, and practices are as efficient, accurate, and effective as possible. This is done by (surprise, surprise) periodically examining and improving your processes to smash bottlenecks, using the best software, and taking advantage of the most efficient methods.
If you’ve ever heard of lean, kaizen, Six Sigma, or DMAIC, then this will sound familiar, as continuous improvement is based on similar principles and forms a key part of both of those practices. This is because the primary objective of any changes is to reduce waste and streamline your work.
While there are many different methods for achieving continuous improvement (such as process innovation and the Deming cycle), all can be classified into one of two groups: incremental or breakthrough improvements.
Incremental vs. breakthrough improvements
Continuous improvement is largely practiced using two disciplines: incremental and breakthrough improvements.
These can be used interchangeably, but the best way to deploy a thorough continuous improvement program is to combine the two. By doing this you can quickly deal with smaller issues while giving larger items the care and attention they deserve.
Incremental continuous improvement
Incremental continuous improvement is all about making small tweaks to a process, method, or practice to improve it as problems are found. This usually costs less and can be done much faster than using the breakthrough method, but there are a few risks and downsides to doing so.
Imagine that you’re working through a regular documented business process (such as client onboarding for a marketing agency) when you come across a problem. It’s not a big enough issue that you need to drop everything and hold a meeting to consult your team about it, but if left alone it could cause confusion for the next person performing the process.
In this case, it’s much better to correct the mistake yourself and make a note to bring it up at your next meeting. That way you can continue through the process without grinding operations to a halt or interrupting someone else’s work.
This is incremental improvement – making small changes or corrections to a process or method without having to review the entire operation. For example, you could correct a spelling mistake or update a link in the process template to make sure that the operation continues to run smoothly and help your team stay at peak efficiency.
Again, while this is generally the quicker and cheaper of the two methods, you run the risk of ignoring how much your changes will affect by not including the rest of your team. That’s why you need to be certain that your changes will only improve the process in some small way, and mention what you’ve done at your next team meeting.
Breakthrough continuous improvement
Breakthrough continuous improvement involves making large changes to a process or method, usually by reviewing the item with the rest of your team and deciding on what to do as a united front. This tends to cost more (in money and time) than incremental improvement, but results in bigger revisions and is sometimes necessary for processes which need to significantly change to remain relevant and accurate.
For example, let’s take our client onboarding for a marketing agency example again. You’ve incrementally updated the process to correct spelling mistakes and keep things running smoothly, but then your team wants to change the questions that are asked to clients during the pre-meeting stage. This more significantly affects the process, and so a large update is needed to make sure that it’s still relevant and useful.
As such, you’ll need to call a team meeting for everyone involved or affected by the client onboarding process. This will let everyone see what needs to change and make their own suggestions based on their experience and current practices.
Sure, it’ll take longer than going in and changing the process yourself, but by hosting a breakthrough meeting you’re letting everyone stay up to date while making sure that the process is as good as it can be with the new developments.
The benefits of continuous improvement
The benefits of continuous improvement are simple; it lets you constantly better your practices to make your team and business more efficient, accurate, and effective.
Let’s say that you’ve already documented your processes and are enjoying the level of consistency this gives. Every task is performed the same way every time, and so it’s easy to predict, track, and ensure a certain level of success.
Despite this, nothing is perfect. There will always be room to improve your processes and methods, be it through small tweaks or re-engineering the whole approach to supercharge your operations.
Is a new employee confused by the instructions for a task? Improve them so that every new hire (and maybe some existing employees) will understand their duties better and get up to speed quicker. Is your current toolkit or software letting you down in some way? Swap it out for something better to let your team scale with your success.
It’s a simple concept, but the effect of having a set program for bettering your processes is so great that there’s practically nothing that can’t benefit from it.
However, with such a simple (and potentially vague) concept, it can be hard to know how to reach those benefits. How exactly should you go about improving your processes and practices to make sure that you’re not, in fact, making things worse?
How to deploy continuous improvement
While it’s entirely possible to use continuous improvement by altering your processes and methods whenever you notice a mistake or bottleneck, it pays to have a set plan to follow. A process for improving your processes, if you will.
Thankfully, the method for doing this is simple:
- Make small, incremental tweaks on the fly.
- Arrange a meeting to discuss larger changes.
- Clearly identify the problem or improvement.
- Plan potential solutions.
- Test changes in a non-live environment.
- Monitor changes after deployment.
Or, if you prefer acronyms, it can be shortened to “TIPTD”:
- Tweak
- Identify
- Plan
- Test
- Deploy
Make small, incremental tweaks on the fly
Incremental improvements are easy to handle, as all you have to do is make the change when you spot the problem. The trick comes with knowing when a change is small enough to avoid bothering the rest of your team.
The easiest way to do this is to ask yourself two simple questions:
- “Would I want to discuss this change if someone else was deploying it?”
- “Could this cause any problems or confuse my team?”
If the answer to both of these is “no”, then go ahead and deploy the change immediately. Remember to make a note to mention the change in your next meeting though, as this will make sure that everyone is up to date on the state of your process.
Arrange a meeting to discuss larger changes
If the answer to either of those questions was “yes” then you’re going to have to put off any changes until you can arrange a meeting with everyone involved in the process.
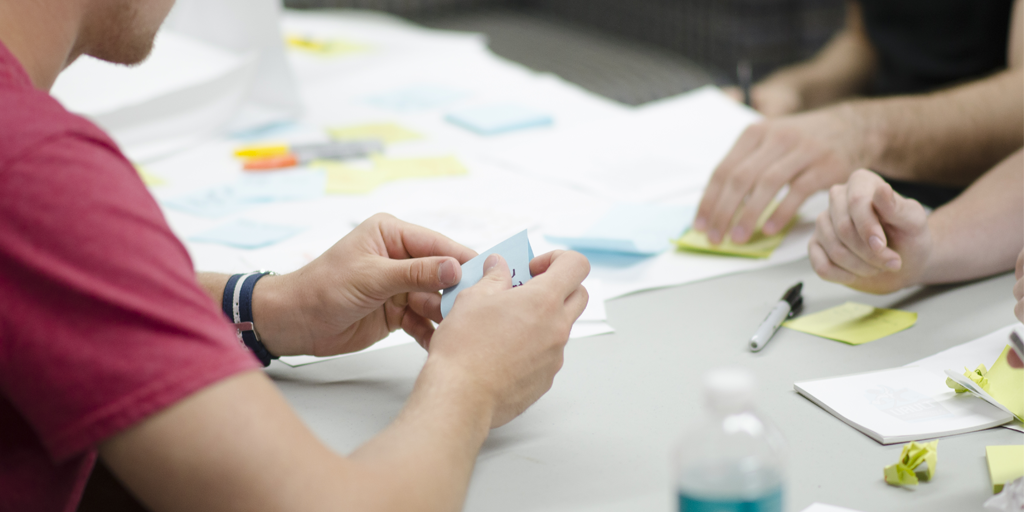
Significant changes need this level of care for two reasons:
- Large changes made without consultation confuse everyone and lead to mistakes.
- You might not be able to predict everything the change will affect.
As soon as you find a problem or change that you think would be beneficial, arrange a meeting with the team who performs the process. This should be as soon as possible, as the process will remain broken (or, at best, inefficient) until you can talk about what’s wrong and correct it.
In the meantime, if the problem is a damaging one then create a temporary solution which will plug the hole and let your team know what you’ve done. If you want to suggest an improvement instead of fix a flaw, wait until the meeting to change anything.
Clearly identify the problem or improvement
In the meeting, it’s important to clearly identify the problem that needs solving or improvement that needs making.
There’s no special trick here, other than making sure that everyone who is affected by and uses the process in question clearly understands what’s wrong with the current process. At the very least you (as a group) need to agree on:
- What the problem/improvement is;
- The issue’s scope (where it starts and ends);
- What it affects, and how;
- Which processes or operations may have already been affected by this issue;
- Whether the affected issues were important enough to warrant damage control or extra attention.
Once you’ve got that cleared up you can move onto the next step of the meeting…
Plan potential solutions
After clearly identifying and defining what needs to be changed, the team needs to agree on the best solution to the issue.
If it’s a problem, mistake, bottleneck, or hole in the process, everyone needs to work together to plan out the best way to fix it. For example, if a packing team is struggling to pack boxes for delivery fast enough, it might be better off changing their method to one piece flow instead of batches.
If an improvement is being suggested to an already functioning process or practice then it’s going to take a little more work from whoever put it forward. In this case, it’s up to them to convince the rest of the team why the change would be worthwhile and why it’s worth uprooting the current method.
For example, if you wanted to suggest managing your operations with business process management software (like Process Street) instead of tools like Microsoft Word, you’d need to list the huge number of benefits of doing so. After hearing how much easier it would be to document, manage, edit, automate, and track your processes and tasks, there should be little question that the change is worth it.
Test changes in a non-live environment
Once the changes are decided it’s a good idea to test them instead of deploying everything straight away. The best way to do this is to try and emulate a live environment and monitor performance relative to the original process.
While it’s not always possible to do this, by testing the changes before committing to them you’ll be able to catch any problems with the new method that weren’t predicted in the meeting. A lot can change when taking processes from theory to practice, and now is the best time to avoid creating more potholes than the one being repaired.
Monitor changes after deployment
Once the changes have been made all that’s left to do is deploy and monitor the process going forward. If everything was tested thoroughly then there shouldn’t be any issues, but again, there’s always a chance that any changes will break something further down the line or cause long-term issues. It’s a good idea to have a risk management strategy on hand for this stage in case problems do crop up that weren’t evident during testing.
If nothing goes wrong then it’s time to move onto the next process and apply continuous improvement all over again. Otherwise, you’ll need to call another team meeting and go back to the drawing board for the latest problem to surface.
Improvement resources to dive deeper
Continuous improvement may be a simple concept, but in practice, there are hundreds of ways in which you can carry it out, and many hundreds more mistakes that can ruin an otherwise solid plan. However, with at least the basic care and measures laid out above you can improve your processes without running that risk.
Still, even your continuous improvement model will have room to be streamlined and tweaked for peak effectiveness. To aid in this persistent task, check out our other resources on similar topics. We’ve covered process improvement, change management models, and everything in-between, and all of it is free to read!
- Process Improvement: Stop Bad Processes Killing Your Business
- How to Use The Deming Cycle for Continuous Quality Improvement
- Business Process Reengineering: What to Do If Your Business Is Failing
- 9 Lean Manufacturing Principles to Kill the Jargon and Get Quality Results
- What is Muda? The 7 Wastes Every Lean Business Needs to Combat
- DMAIC: The Complete Guide to Lean Six Sigma in 5 Key Steps
What does your continuous improvement process look like? What causes the biggest problems? I’d love to hear from you in the comments below!
Ben Mulholland
Ben Mulholland is an Editor at Process Street, and winds down with a casual article or two on Mulholland Writing. Find him on Twitter here.